All of the Toyota Manufacturing Techniques In The Lean Startup
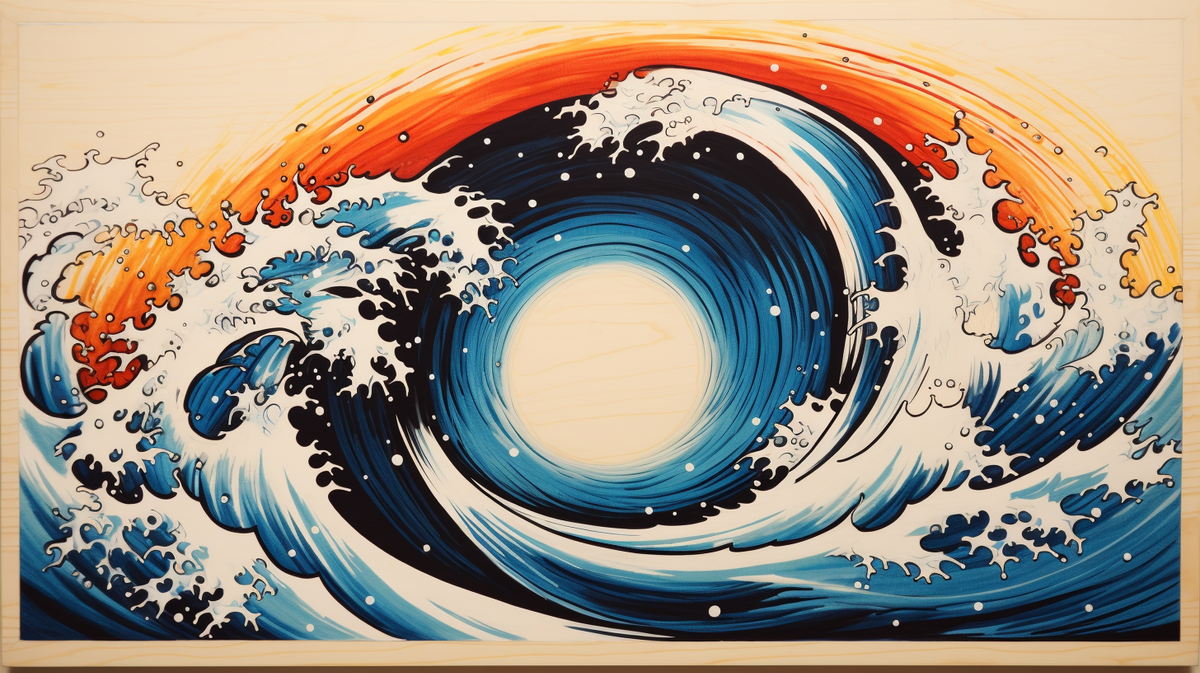
I recently read The Lean Startup by Eric Ries. The book lays out a framework for startups that is based on quick iteration and constant learning. As a developer I have seen and worked with lean processes, but applying those same principals to management and innovation is very exciting and makes for a great read.
Much of the book draws inspiration from traditional manufacturing, and one of my favourite parts of the book are the specific references to Toyota's lean manufacturing techniques. Toyota and their Production System has remained relevant since it's inception in 1948.
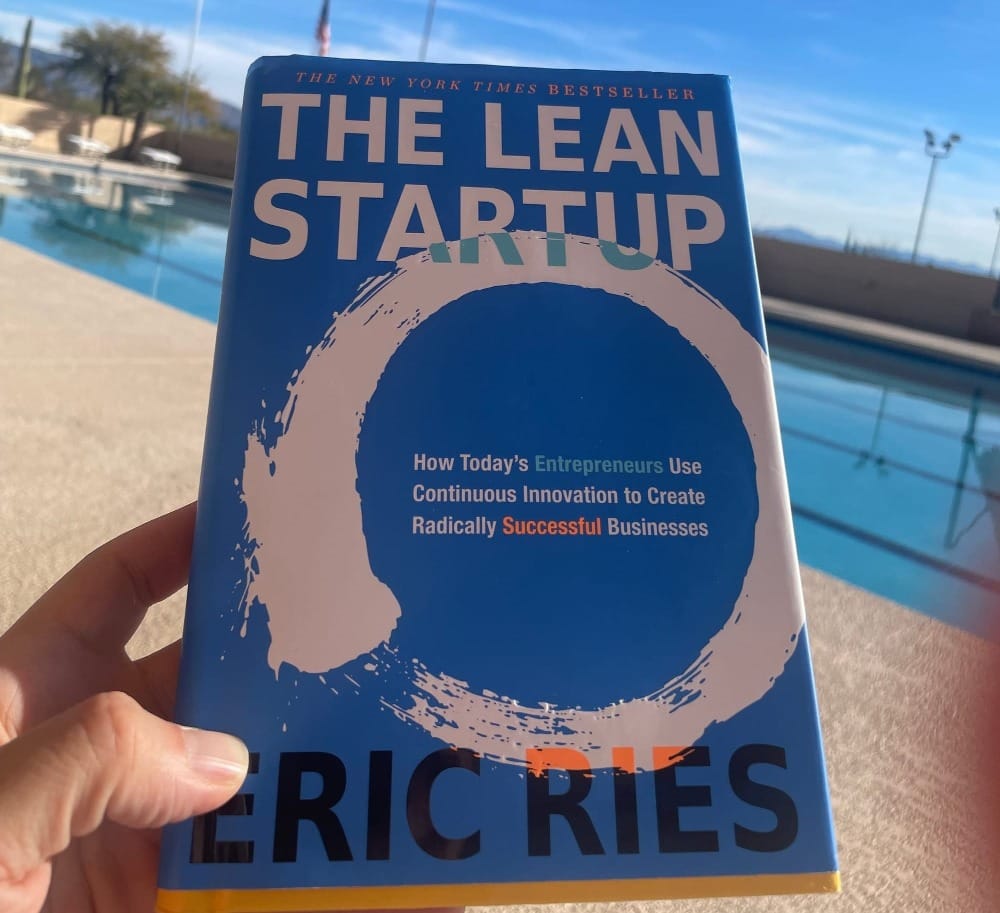
The Toyota Production System (TPS): Ries highlights Toyota's revolutionary production system, which is the backbone of lean manufacturing. TPS focuses on eliminating waste, improving process efficiency, and achieving just-in-time production. This system prioritizes quality and efficiency, ensuring that resources are only used as needed and defects are minimized. A good reference point is the Toyota Way which lists 14 different principles that TPS works towards.
The Five Whys: This is a technique borrowed from Toyota used to explore the cause-and-effect relationships underlying a particular problem. Essentially, it involves asking "Why?" five times to drill down to the root cause of a problem. Ries adapts this technique to the Lean Startup methodology as a tool for startups to use in identifying the underlying issues behind failures or setbacks, rather than just addressing the most immediate symptoms. This approach promotes deeper understanding and more effective solutions. I have seen this work well, but the most important part (and Ries stresses this in the book) is that all relevant stakeholders should be present, otherwise you may descend into "The Five Blames."
Andon Cord: Toyota's assembly line workers have a literal cord that when pulled stops production if they encounter a significant problem. This practice ensures that issues are addressed promptly and that the final product meets the company's high-quality standards. Ries uses this example to illustrate the value of empowering team members to signal problems immediately and halt processes if they believe something is wrong. In the context of Lean Startup, this translates to creating an environment where feedback is actively sought and acted upon quickly by using small batches, ensuring that the product development process remains agile and responsive to issues as they arise.
Kaizen (Continuous Improvement): Kaizen represents the philosophy of continuous, incremental improvement and learning. In "The Lean Startup," this principle is crucial as it encourages startups to constantly test their visions against reality, learn from mistakes, and systematically improve their products, processes, and business strategies. The iterative cycle of build-measure-learn is at the core of the Lean Startup methodology. Ries provides some great examples from his personal experience building and scaling IMVU and shows you how to approach cohort analysis in the book.
Genchi Genbutsu (Go and See): This term translates to the idea that one should go and see the problem in person to truly understand it. Ries adapts this concept for startups as direct customer engagement and observation. By understanding customers' actual problems and needs, startups can develop products that better solve real-world issues. At Toyota, Ries tells us about the chief engineer for the second generation Sienna minivan who personally drove fifty thousand miles across North America to test things out before getting started.
Muda (Waste): Muda refers to any activity that consumes resources but creates no value for the customer. In the book, Ries identifies the different forms of waste that can occur in a startup, such as building features that no one wants or not releasing a product in time to get customer feedback. The Lean Startup methodology aims to eliminate Muda through the Minimum Viable Product (MVP) concept, where the focus is on developing a product with just enough features to satisfy early adopters and provide feedback for future development. There is a wonderful story about a travelling washing machine in the back of a pickup truck that was the MVP for a laundry pickup and drop off service.
Kan-ban (card you can see): I know kan ban as a way to organize work for a software project into columns such as Pending, To Do, Finished, Approved, Checked, Etc. but while reading this book I realized that kan ban was invented for supply replenishment in manufacturing and industrial supply chains. It's amazing to me to think about a kanban board where the cards represent the current physical location of supplies / products. The story in the book of Toyota about adjusting inventory levels based on consumer consumption is a fascinating example of "just-in-time" distribution and serves as a powerful metaphor for software development and innovation.
Overall, I enjoyed this book. I would recommend it to anyone involved in disruptive work or innovative creation. Some advice that carries throughout the book is that you should start making money as soon as possible and if at all possible, charge people right away. Their wallets are better indicators than any survey response.